Wood Work
Description
Japan is home to a wide range of climates and trees. Since ancient times, people have used wood to make quality dishes, boxes, and other articles. Woodwork is the art of creating articles and utensils that emphasize the beautiful grain patterns characteristic of wood. As a result, the process of selecting the wood is a crucial starting point for any piece of woodwork.
Process
- STEP 1The wood is selected
- STEP 2
- Wooden panels are joined together
- The wood is hollowed out
- The wood is turned on a lathe
- The wood is bent
- STEP 3Finishing touches
Artistic Techniques
Wood joinery
In wood joinery (sashimono), wood boards are cut into panels with care to how the grain patterns will fit together in the final piece. The wooden panels are then cut or carved to create interlocking joints. These joints, which are the key feature of wood joinery, make it possible to connect boards at right angles to produce boxes and other articles. Wood joinery is assembled without the use of nails or any other metal hardware.
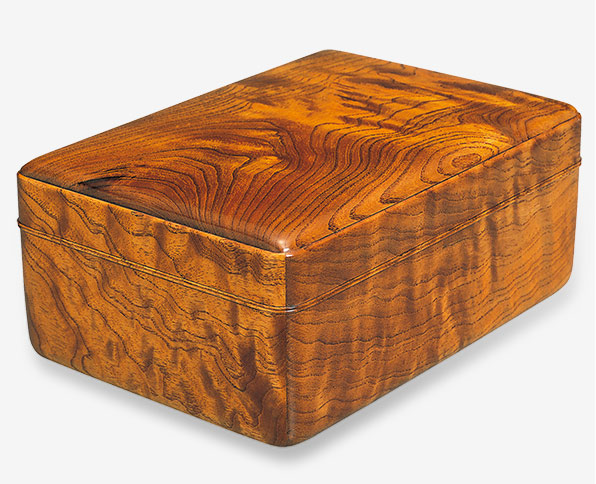
Hollow work
In hollow work (kurimono), gouges and chisels are used to hand-carve hollow vessels from a block of wood. Complicated curves and rounded forms are a common feature of hollow work.
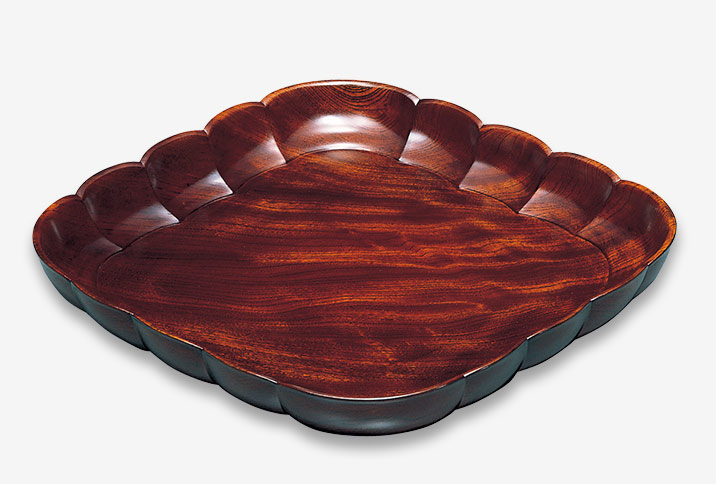
Wood turning
In wood turning (hikimono), a piece of wood is rotated on a lathe and shaped with various cutting tools. Wood turning is suited to the creation of round trays, containers, and bowls. Different blades and cutting angles can be used to produce a wide range of forms. Balanced, symmetrical forms are made by spinning the lathe at a constant speed.
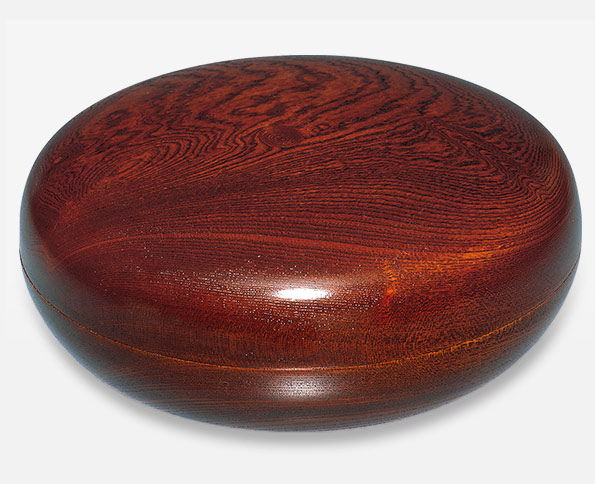
Bentwood work
Japanese bentwood work (magemono) is predominantly produced using one of two methods. In the first method, thin strips of wood are softened with steam and bent into cylindrical forms. In the second method, notches are sawed into the back side of wood strips, and the strips are bent into polygonal forms.
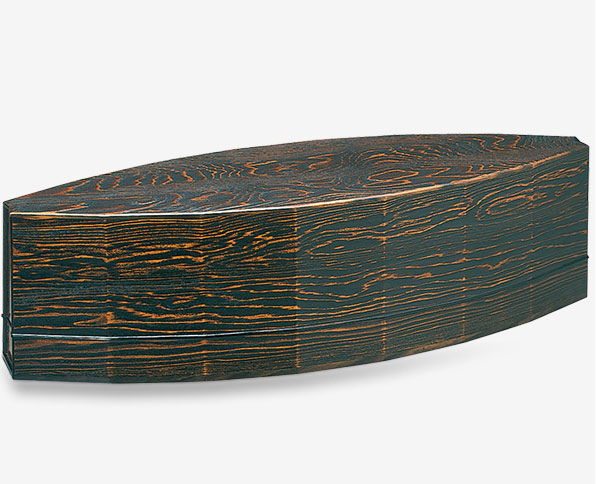
Wood inlay
Wood inlay (moku zōgan) is a decorative technique in which wood, metal, or shell is inserted into cavities cut into a wooden substrate to produce contrasting designs.
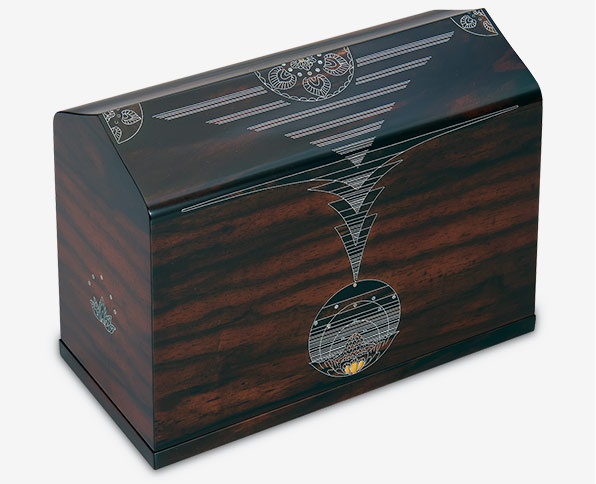
Mokuga wood decoration
Mokuga (“wood picture”) is a decorative technique in which slices of wood several millimeters thick are cut into geometric pieces such as rectangles or triangles and then attached to the surface of an object to create a design. Complicated works may use over one thousand small parts, carefully arranged with attention to the alignment of the grain.
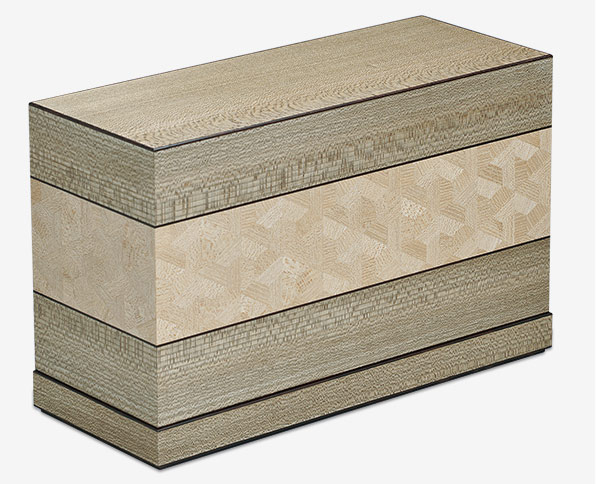
Wiped lacquer finish
Wiped lacquer (fuki urushi) is a wood-finishing technique consisting of a thin coat of lacquer. The lacquer is applied with a spatula or brush, rubbed in with a cotton cloth, and then wiped away using washi paper or clean fabric. Repeating the process numerous times produces a finish that brings out the wood’s grain and texture.
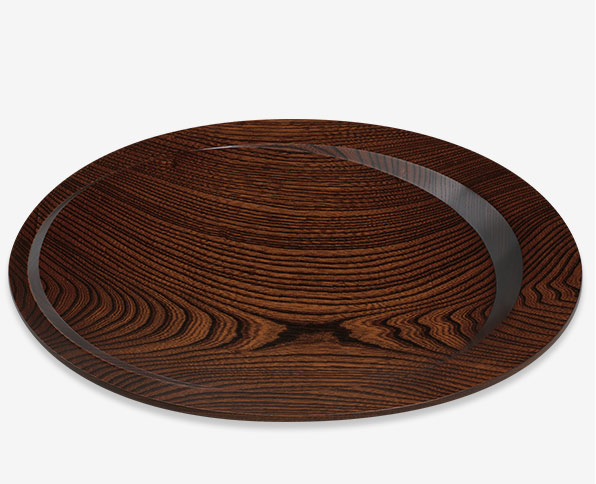
Bamboo Work
Description
Of the over six hundred varieties of bamboo that grow in Japan, only ten or so are used for bamboo work. Bamboo is pliable, resilient, and does not break easily. Due to these qualities, bamboo has been used to make daily tools and utensils since prehistoric times. Large numbers of flower baskets and offering trays made from bamboo are preserved among the artifacts at the Shōsōin Repository in Nara.
The traditional techniques of bamboo work are still practiced today, and beautiful bamboo objects and utensils play an important role in the tea ceremony, ikebana flower arranging, and interior design.
Process
- STEP 1Thin strips of bamboo are prepared for weaving
- STEP 2
- The bamboo strips are plaited together
- Constructed bamboo elements are interlaced
- STEP 3Finishing touches
Artistic Techniques
Plaited bamboo
Plaited bamboo basketry (amimono) is created by weaving together hundreds of strips of bamboo into patterns known as plaiting (ami). Various patterns and shapes can be created by using bamboo strips of different widths or thicknesses. The many styles of plaiting utilize bamboo’s pliability to produce beautifully patterned works.
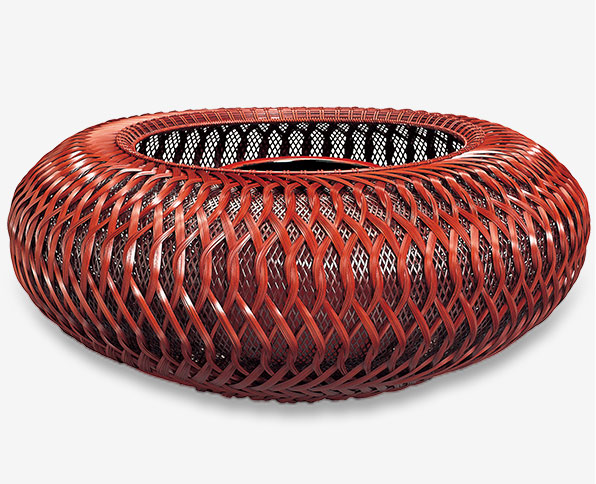
Parallel construction
Parallel construction (kumimono) is a method of bamboo basketry in which separately prepared bamboo components made of parallel elements are interlaced. The components are constructed using a technique called “comb plaiting” (kushime-ami), in which thicker, sturdy strips of bamboo are evenly spaced, and then the edges are tied together with rattan.
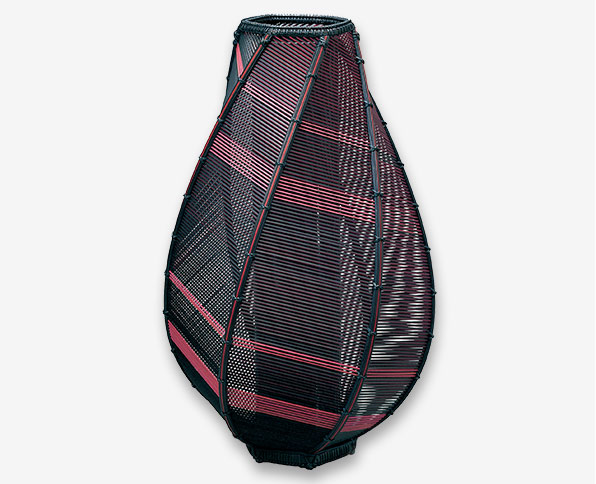
Wood And Bamboo Artists
Main Production Areas
Kyo wood joinery Open in new window
Kyo Wood Joinery is a woodwork produced in Kyoto Prefecture. Various types of furnishings including paulownia products, as well as tea ceremony and lathe turned items are produced. Wood joinery is a general term for furniture and furnishings made by assembling wood without using metal nails etc.
Nagiso woodturning Open in new window
Nagiso Woodturning is a woodwork produced around Nagiso Town, Kiso County, Nagano Prefecture. Plain wood products are made by planing the raw wood cut in round slices while turning on the lathe. It is known for its beautiful wood grains.