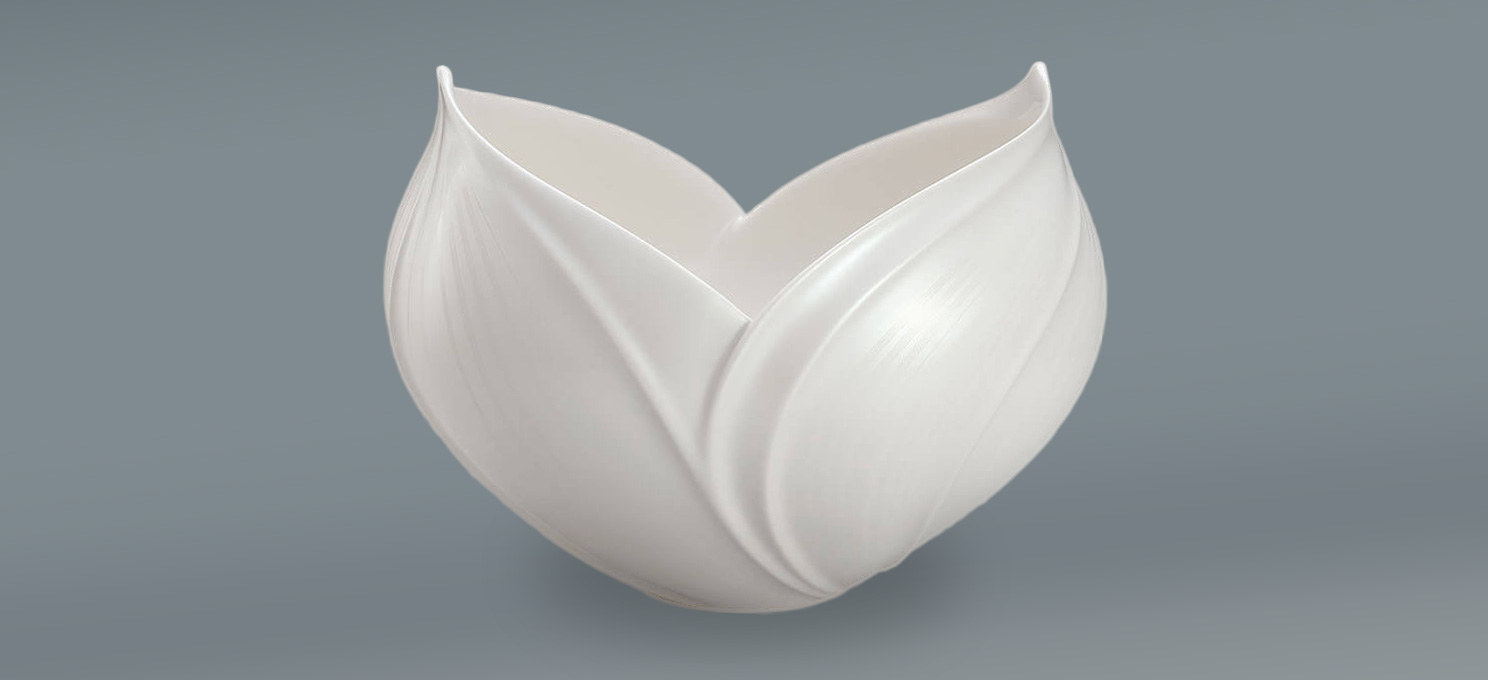
Description
Ceramics (yakimono) can be divided into two main types by material: earthenware/stoneware (tōki), which is predominantly made from soil-based clay, and porcelain (jiki), which is made from mineral-based clay. The materials are mixed with water to produce clay. The resulting clay is formed into dishes, pots, vases, or other items that are then fired at high temperatures in a kiln. Japan’s ceramic traditions developed in accordance with the clay of each region, and as a result, many of the crafts bear the name of the region where they were made.
Process
- STEP 1Clay preparation
Quality soil or stone is gathered and made into clay.
- STEP 2Shaping
A potter’s wheel is used to shape round dishes, pots, and vases. Other common methods include hand-layering coils of clay to create forms or hand-building three-dimensional objects from thin slabs of clay.
- STEP 3Bisque firing
Unglazed pieces of pottery are fired at temperatures between 600℃ and 950℃ , which hardens them and makes them easier to glaze.
- STEP 4Glazing
The surface of the pottery is coated with a glaze that vitrifies when fired, producing a layer of glass over the piece.
- STEP 5Kiln firing
The length of time and temperature of firing varies depending on the type of clay and the glaze applied. After the piece has been fired and hardened, it is complete.
Artistic Techniques
Iron underglaze
Iron underglaze decorations (tetsu-e) are achieved by painting designs in a pigment containing iron oxide. The piece is then coated with a transparent glaze and fired at a high temperature. This basic method of ceramic underglaze decoration relies on the color changes displayed by iron oxide when it is exposed to heat.
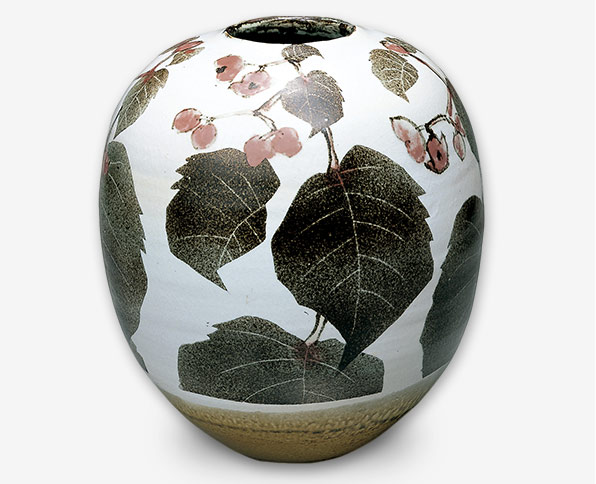
Blue underglaze
Blue and white porcelain (sometsuke) is made by painting blue underglaze decorations on white bisque-fired pottery using a cobalt-rich pigment known as zaffer (gosu). The piece is then coated with a transparent glaze and fired. This technique for making blue and white porcelain has been used in China since around the twelfth century during the Yuan Dynasty.
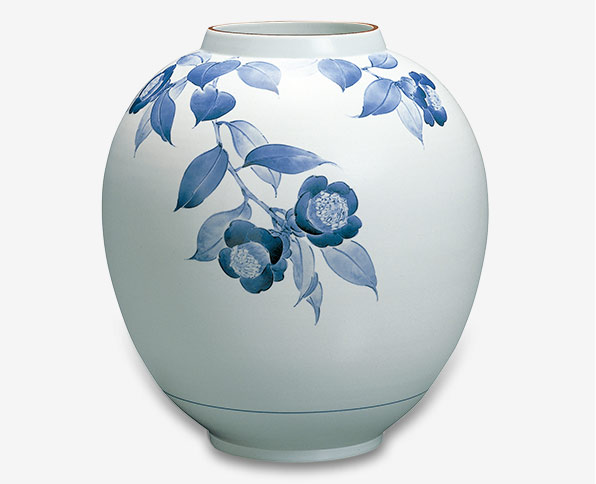
Overglaze enamel
Overglaze enamel decorations (iro-e, literally “colored pictures”) are achieved by applying designs to the surface of already glazed and fired porcelain. The decorations are painted over the glaze, and the piece is fired again at a low temperature of approximately 800℃. The pigments used in traditional overglaze decorations are known as wa enogu (“Japanese paints”) and offer a palette of colors such as red, blue, yellow, green, and purple. Overglaze enameling may also be done with Western pigments (yō enogu).
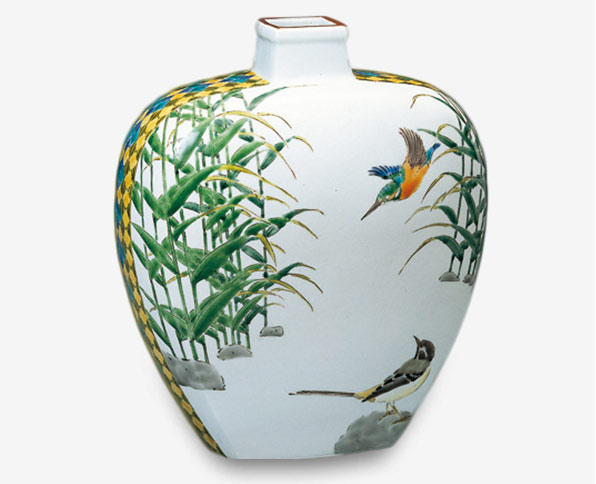
Pale blue porcelain
Pale-blue celadon porcelain (seihakuji, known as qingbai in Chinese) is made from porcelain clay derived from white stone. The porcelain is bisque fired and then covered with a glaze containing minute amounts of iron, which turns a blue tint when fired. Celadon originated in China. White porcelain made with a glaze that turns transparent when fired is called hakuji (“white porcelain”), while pieces made from porcelain clay containing iron and coated in a glaze that turns a bluish-green when fired is called seiji (“celadon” or “green ware”).
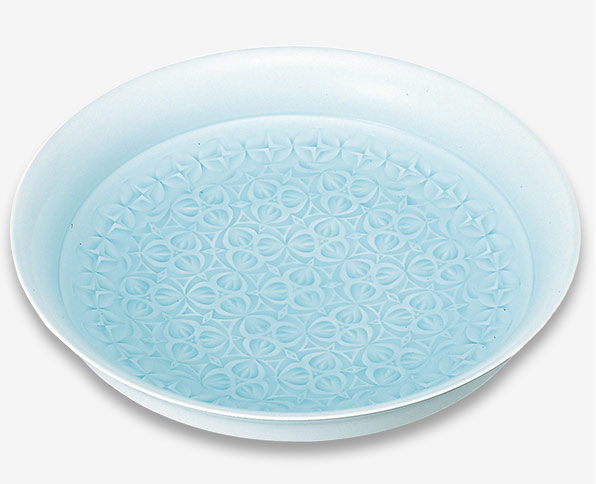
Inlay ceramics
Inlay (zōgan) ceramics are created by making incisions on the surface of a piece which are then filled with a differently colored clay to create a design. After the clay is inlaid, a glaze is applied and the piece is completed upon firing.
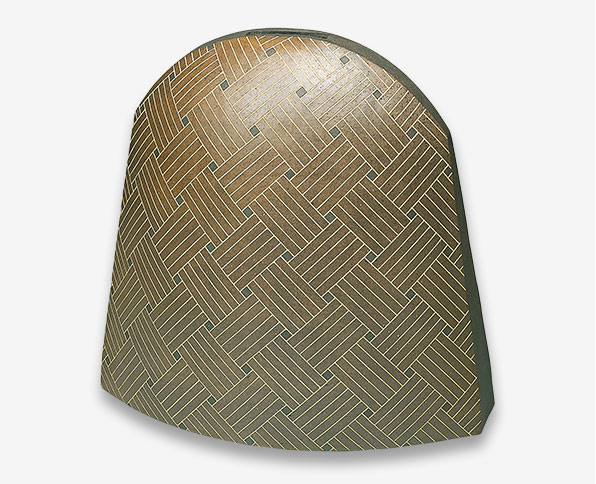
Marbleized clay
Marbleized clay (neriage) ceramics are made by layering or combining different colors of clay. A wide variety of patterns can be produced depending on how the clays are combined, with the cross-sections of the finished pattern appearing on the surface of the piece.
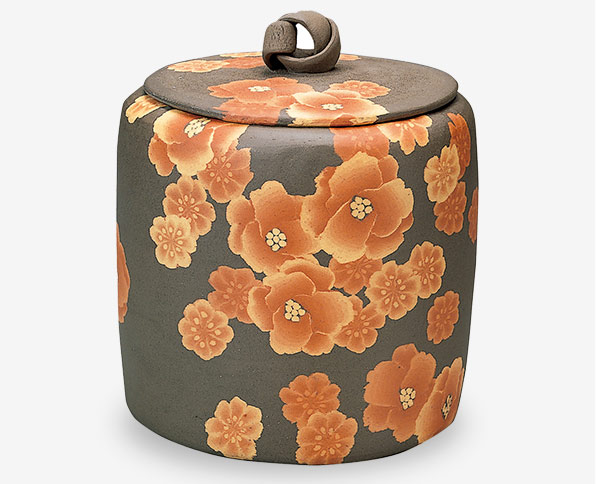
Bizen ware
Bizen ware is a type of high-fired unglazed (yakishime) stoneware made near Bizen in Okayama prefecture. The local clay, called hiyose, resists the application of glaze, so vessels are fired uncoated at high temperatures for long durations. The resulting pottery is well vitrified and features earthen tones and natural ash effects. Ceramists can induce a rich variety of expressions by arranging pieces within the kiln and influencing how they interact with the charcoal and ash. Every piece of Bizen ware is unique.
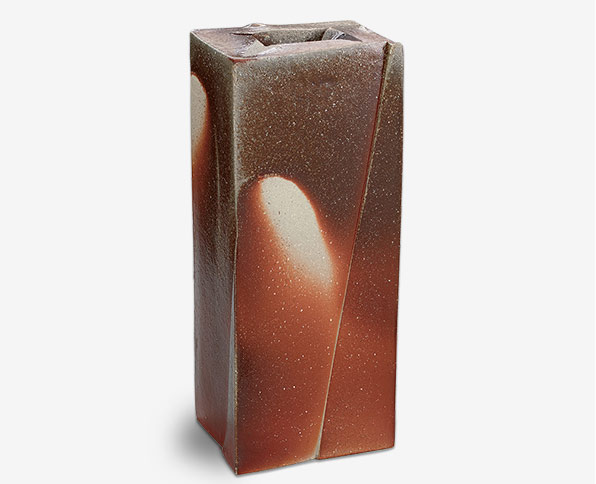
White porcelain
White porcelain is made from a pale clay of pulverized pottery stone coated in a transparent glaze. Porcelain from China’s Song dynasty is especially famous. Japanese production began in the early seventeenth century in Arita on the island of Kyushu. White porcelain is frequently used as a base for overglaze enamels (iro-e) and blue-and-white (sometsuke) ware.
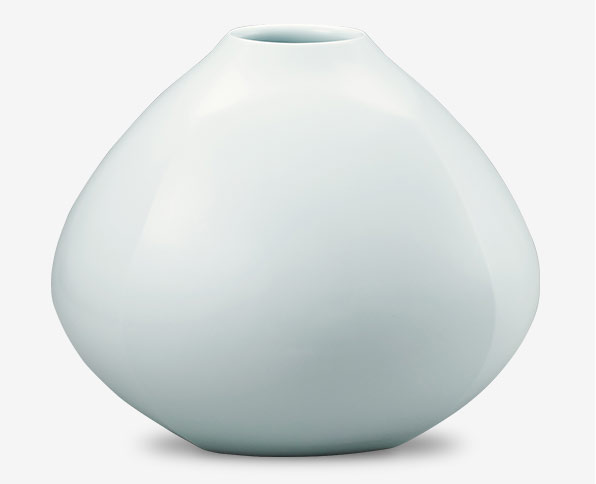
Ink resist decorations
Ink resist (sumihajiki) techniques developed in the seventeenth century as a method for reserving white spaces in designs on Nabeshima ware, a type of high-quality gift porcelain fired in the Saga Nabeshima domain’s official kilns. Sumi ink is used to paint designs on the vessel, over which colored pigments are then applied. The ink, which contains animal glue, repels the water in the pigment, preventing it from adhering to the body of the piece. When the vessel is bisque fired, the ink evaporates, leaving behind white designs in its place.
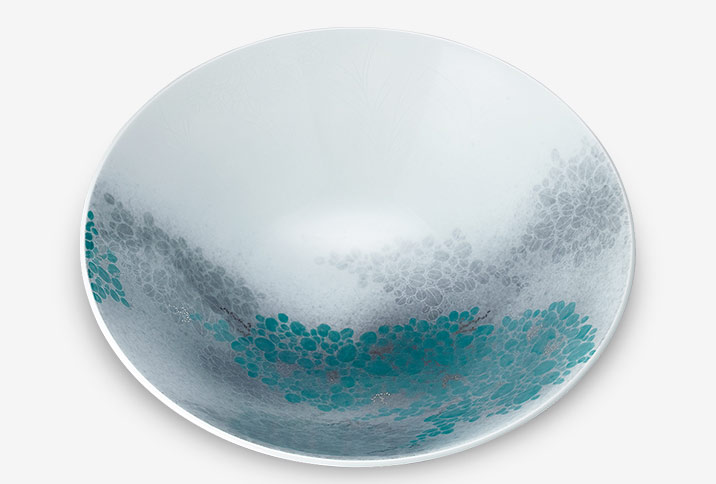
Shino ware
Shino ware consists of vessels of eggshell colored clay (mogusatsuchi) thickly coated in an opaque, milky-white feldspathic glaze.
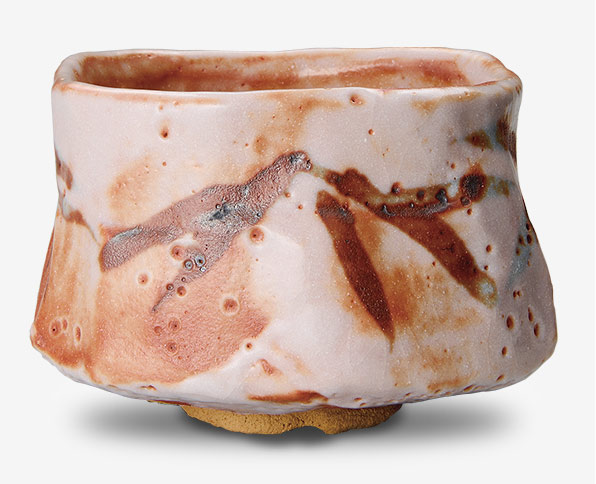
Iron glaze
Iron glaze (tetsuyū) refers to a broad category of iron-rich ceramic glazes. Depending on the iron content, these glazes can produce colors ranging from black to brown to amber. Blackish glazes with around five percent iron content are known as Tenmoku (Ch. Jian ware) glazes.
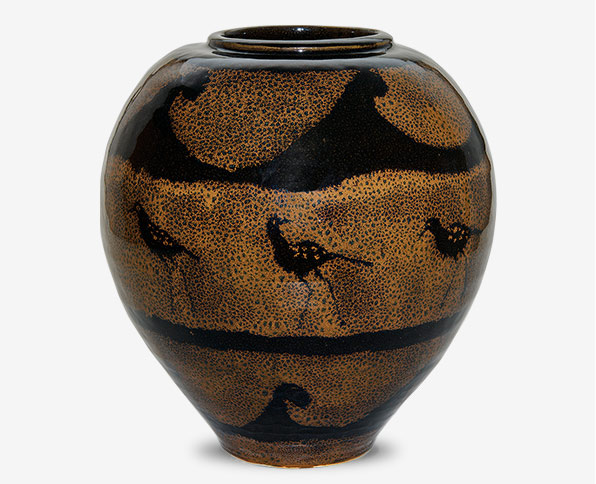
Underglaze gold
Underglaze gold (yūri kinsai) is achieved by applying designs in gold leaf or gold pigment to a glazed surface, which is then coated in a second, transparent glaze and fired. Because more than one variety of glaze is used to encase the gold, the firing temperature must be closely controlled, and the process demands significant skill. The outer layer of transparent glaze protects the gold and gives it a pleasing, muted appearance.
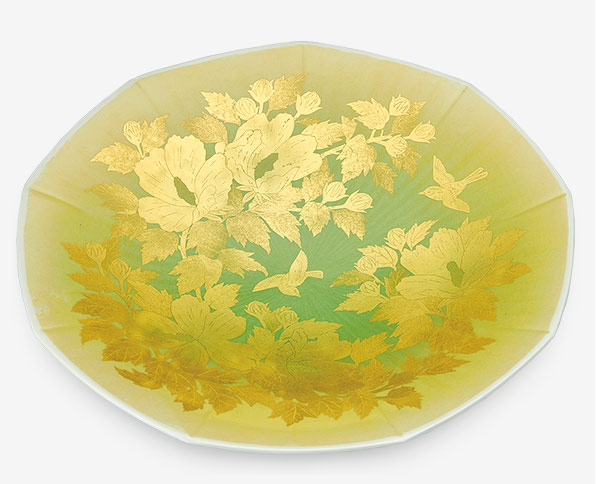
Hagi ware
Hagi ware is a type of pottery predominantly made around the cities of Hagi, Nagato, and Yamaguchi in Yamaguchi prefecture. Vessels are made with Daido clay, Mitake clay, and Mishima clay. The resulting stoneware is rarely decorated with motifs, as the texture and qualities of the clay are key points of visual interest that appeal to tea ceremony practitioners.
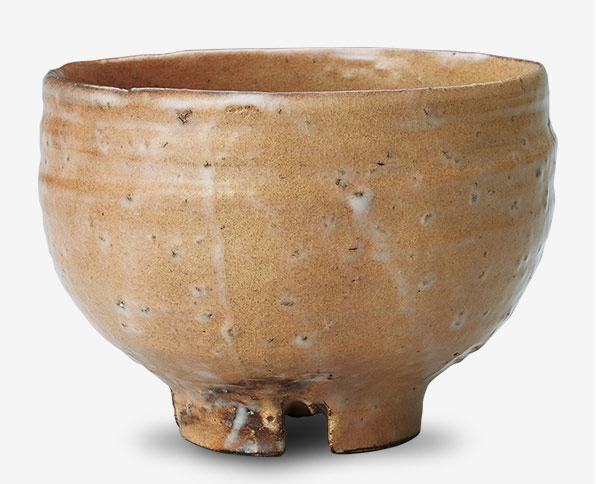
Ash glaze
Ash glazes (kaiyū) are ceramic glazes made from the ashes of plants, such as wood or straw. Traditionally, these are divided into three categories: pure wood ash, which is made from the bark of trees such as oak and chestnut and has a faintly blue hue; hearth ash, which contains impurities and has a faintly bluish-green hue; and straw ash, which produces a milky-white glaze.
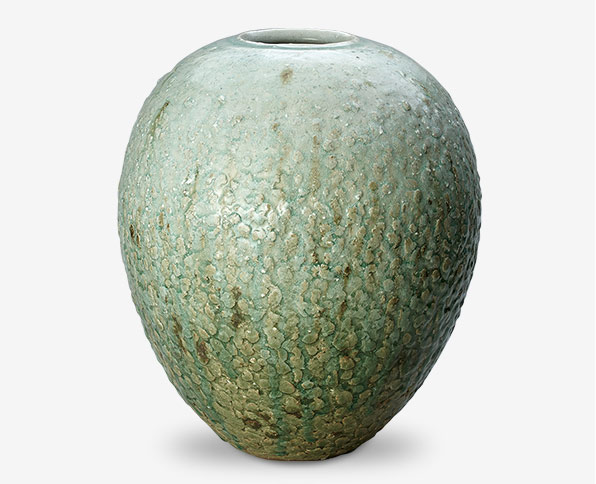
Celadon
Celadon (seiji) is a light blue-green pottery, usually porcelain or stoneware, produced by reduction firing a transparent glaze containing iron oxide. By restricting or eliminating the supply of oxygen to the kiln, the reduction firing process causes the iron in the glaze to turn bluish-green.
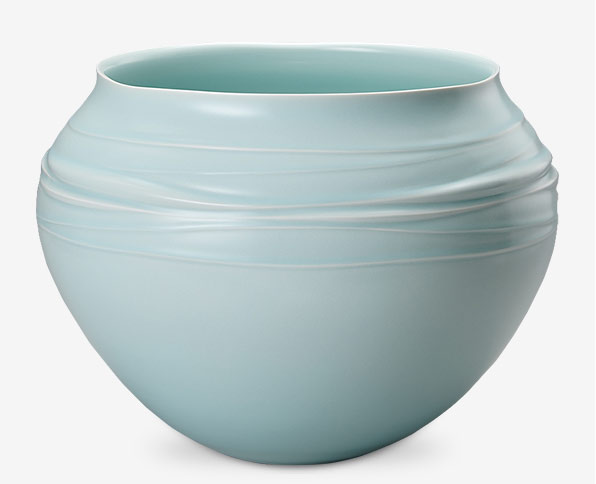
Gold decoration, Silver decoration
Gold and silver decorations consist of motifs rendered in gold and silver pigments or leaf. The decorations may be applied directly to the clay substrate or as an overglaze decoration that is fired onto the vessel. The gold and silver decorations are fired at lower temperatures than underglaze decorations, then polished to bring out their luster.
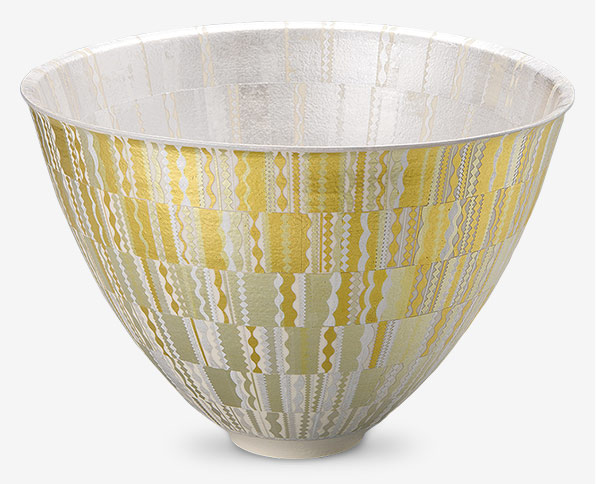
Kiln effects
Kiln effects (yōhen) is a term that describes a wide variety of spontaneous expressions produced by the interaction of the kiln atmosphere and the surface of the vessel during firing, including oxidation and reduction effects. The cracks, flashing patterns, and natural ash glaze effects on unglazed wares such as Bizen and Shigaraki are famous examples of kiln effects.
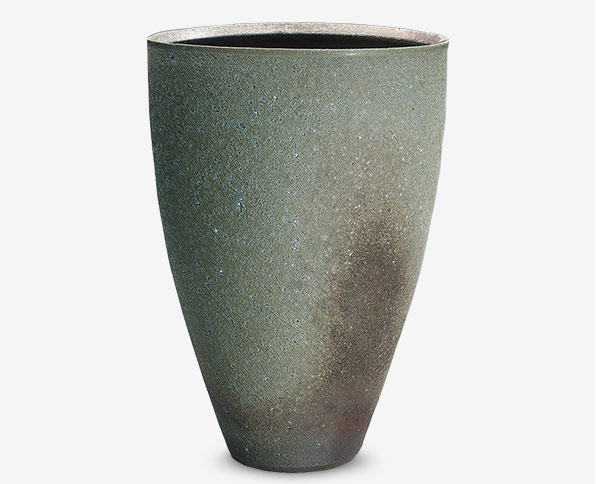
Porcelain underglaze painting
Porcelain underglaze painting (saiji) is achieved by applying colored underglaze decorations to porcelain. The vessel is then coated with a transparent glaze and fired. White porcelain is used to emphasize the painted motifs.
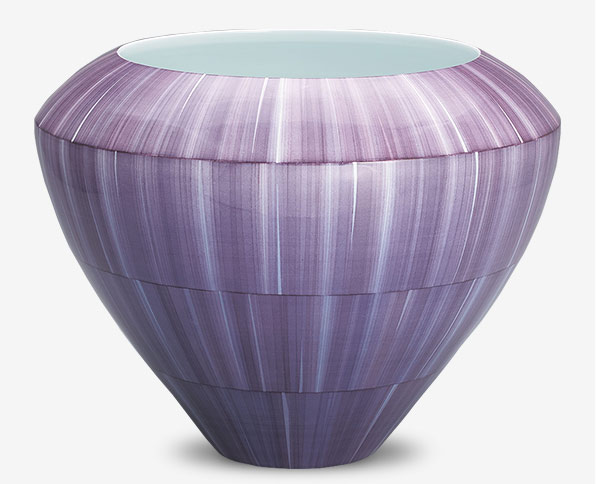
Ceramics Artists
Main Production Areas
Shigaraki ware
Shigaraki ware is a type of ceramics produced around Shigaraki Town, Koka City, Shiga Prefecture.Using coarse clay, it is known for its rustic texture. The natural colors that are created from the ashes adhering to the surface of the ceramics in the kiln adds resonance.
Imari ware / Arita ware
Imari ware / Arita ware are porcelain produced around Arita Town, Saga Prefecture. As they are made from porcelain stone, the texture is smooth, but at the same time they are strong and durable, They are known for the color combination of bright zaffer and red painted on white porcelain.
Kutani ware
Kutani Ware is a porcelain produced in the southern part of Ishikawa Prefecture. It is known for its overglaze decorations using five colors, green, yellow, red, purple and navy blue called gosai to paint flowers, birds and landscapes delicately in bold compositions.
Mino ware
Mino ware is a pottery produced in the Tono region of Gifu Prefecture. Mino ware does not have just one typical style, but a variety of styles. Fifteen types of Mino ware including Oribe, Shino and Kiseto are designated as traditional crafts.